Rotating machinery design and analysis has high and often non-negotiable requirements for efficiency, durability, and reliability.
With these goals in mind, the rotating machinery industry has widely adopted digital prototyping to explore a larger design space than is otherwise cost-prohibitive. But for too long companies have been restricted in deriving the maximum benefits from digital prototyping due to the limitations of desktop-based legacy software, and Hazleton Pumps was no exception.
Hazleton Pumps develops and manufactures heavy-duty pumps and pump systems. Based in South Africa, the company has been serving clients from around the world since 1979.
Hazleton Pumps’ local test facility.
For the design and analysis of their in-house pumps, Hazleton relied on OpenFOAM for computational fluid dynamics (CFD) software and an assortment of tools for computer-aided design (CAD), meshing, and post-processing results. Their simulation workflow was time-consuming and cumbersome, with each step requiring immense manual effort. Project time and cost were further increased by desktop-based computations that did not scale up on-demand and required additional investment in high-performance clusters.
In need of a complementary design and CAE solution, Hazleton turned to Onshape and SimScale. These case studies explore how their cloud-native solution focus enabled Hazleton Pumps to obtain fast and accurate fluid flow and performance assessments for their pump designs.
Parametric Studies for Pump Curve Characterization
Having used OpenFOAM with little success, Hazleton’s Engineering Manager Benjamin van der Walt started investigating Onshape simulation partner, SimScale, in October 2021. Benjamin investigated three pumps using SimScale’s cloud-native technology for rotating machinery, which is capable of solving complex fluid physics for different speed regimes, with or without structural and thermal effects.
This case study will focus on CFD studies for the small- and medium-sized pumps, simulated using an incompressible steady-state approach and a RANS-based turbulence model. The primary objective of the simulations was to accurately calculate and benchmark the performance of the two pump designs.
Case 1: The first pump investigated by Hazleton was a 180 kg, 5.5 kW submersible, as shown below.Pump designs simulated by Hazleton Pumps.
Through simulations in SimScale, they wanted to establish a baseline for the new impeller used in this pump and explore design improvements by analyzing the pump’s performance curve. Typically, a pump curve requires simulating a minimum of six input data points.
In Benjamin’s experience, generating a solution for one input data point using OpenFOAM’s transient AMI approach on a local HPC took about three to six days. The time taken changed to about 9-15 hours with the steady-state MRF approach. This meant that generating a pump curve with six data points took up to a month and produced over a terabyte of data.
Using SimScale’s cloud-native rotating machinery technology, Hazleton Pumps was able to produce the entire pump curve for this model in seven minutes, which is a 99.9% reduction in simulation time compared to OpenFOAM.
Pump Curve for Case 1, with Best Efficiency Point at 14 l/s.
Case 2: In rotating equipment design, solution accuracy is paramount and cannot be sacrificed for the sake of speed. To establish the accuracy of the fast results from SimScale, Hazleton simulated a second model, a 75 kW medium-sized vertical pump.
Hazleton tested the pump in their in-house test facility and generated pump performance data. The simulation set-up in SimScale was exactly the same as the test set-up, taking into account all the pump components like the inlet, impeller, volute, and discharge. Allowing for manufacturing differences and correcting for head loss observed in the pipes, the pump curve results from SimScale were within 2-3% error of test data, as shown below.
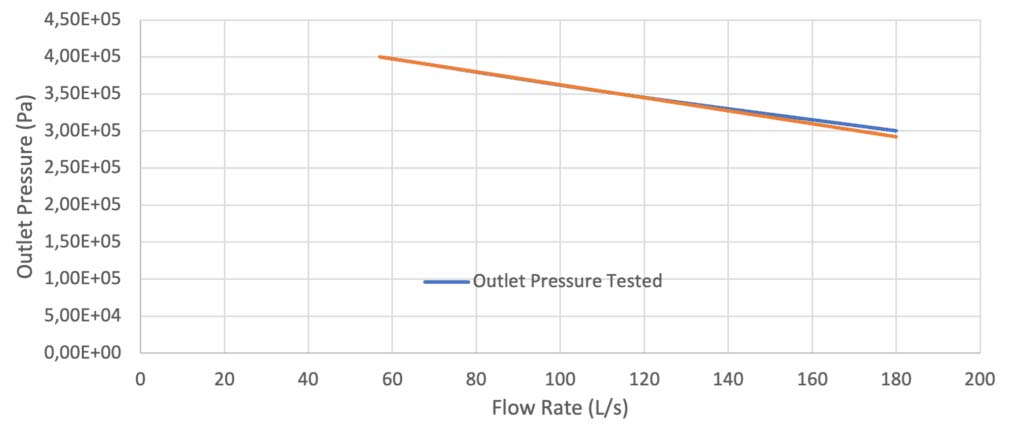
In addition to expedited turnaround for accurate simulation of rotating equipment, SimScale’s proprietary technology also significantly improved Hazleton’s simulation workflow.
With OpenFOAM, Benjamin’s workflow had been extremely complicated and he found the solution to be highly sensitive to the problem set-up and mesh, and therefore, unpredictable. He had to depend on a variety of tools for each step of the process. For example, he used Blender for pre-processing, ParaView for result visualization and Excel for data analysis.
With SimScale’s browser-based platform, Benjamin could perform all steps of the simulation seamlessly, without leaving the easy-to-use interface. Starting with a CAD model, he could generate the mesh, set up the simulation inputs, run a parametric sweep in parallel, and automatically plot the pump curve. To learn more about how Hazleton was able to do this, make sure to watch the free on-demand webinar.
Hazleton and SimScale’s Continued Collaboration
Hazleton Pumps incorporated SimScale’s proprietary CFD technology for rotating machinery into their R&D cycle, with the goal of accelerating the simulation-driven design of their in-house pumps.
Taking advantage of SimScale’s cloud-native simulation architecture and seamless handoff to and from Onshape, Hazleton was able to generate performance pump curves within minutes, cutting their simulation turnaround time by ~100x compared to previously used tools. They also benchmarked results obtained from SimScale with experimental data from their test facilities and found our proprietary solver to be highly accurate and within 2-3% of test data. With the ability to host simulations and related data on the cloud, Hazleton completely eliminated their high-performance computing (HPC) and data management costs. Additionally, their simulation workflow was also tremendously simplified, thanks to SimScale’s browser-based, all-in-one software interface, which can be accessed from anywhere in the world through a simple login.
With such monumental savings in time and cost, Hazleton is now able to focus on designing and building better pumps, faster. SimScale is committed to providing cloud-optimized simulation solutions to Hazleton for further analysis of their in-house pump designs.
Ready to try out Onshape’s cloud-connected partner app SimScale? Head to the Onshape App Store today!
The Onshape App Store
Extend the power of Onshape with integrated
cloud partner apps for Simulation and more.
(A version of this article was published on the SimScale website in March 2021.)